I use a piece of wooden stick on which I glued some felt. I cut the sand paper the same width as the felt and wrap it around. It works perfect - you can see it in the picture.
But nice tip for using old magnet rack for holding the knife. I was clamping it in (on the pic is western Akifusa). This works perfect for western handles and octagonal handles, but with D shaped it is a big problem -> you can not fix it good.
But nice tip for using old magnet rack for holding the knife. I was clamping it in (on the pic is western Akifusa). This works perfect for western handles and octagonal handles, but with D shaped it is a big problem -> you can not fix it good.
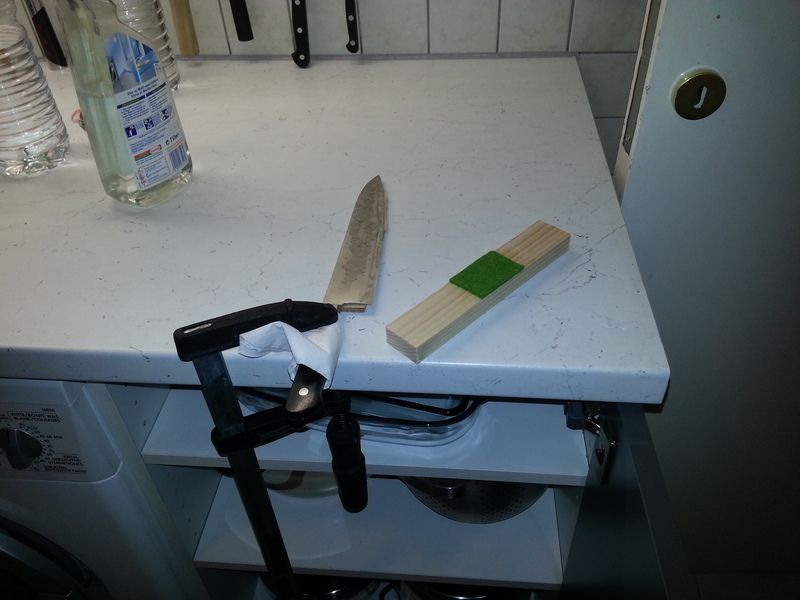