Hello,
This is one I just finished up, the blade is AO super blue, carbon clad. The handle is bog oak with ebony and a stirling silver spacer.
I have been spending quite a bit of time working on grind geometry, and my knives are staring to cut ok now ! (even though the finish on this one is quite agricultural!)
All the best !
John
This is one I just finished up, the blade is AO super blue, carbon clad. The handle is bog oak with ebony and a stirling silver spacer.
I have been spending quite a bit of time working on grind geometry, and my knives are staring to cut ok now ! (even though the finish on this one is quite agricultural!)
All the best !
John
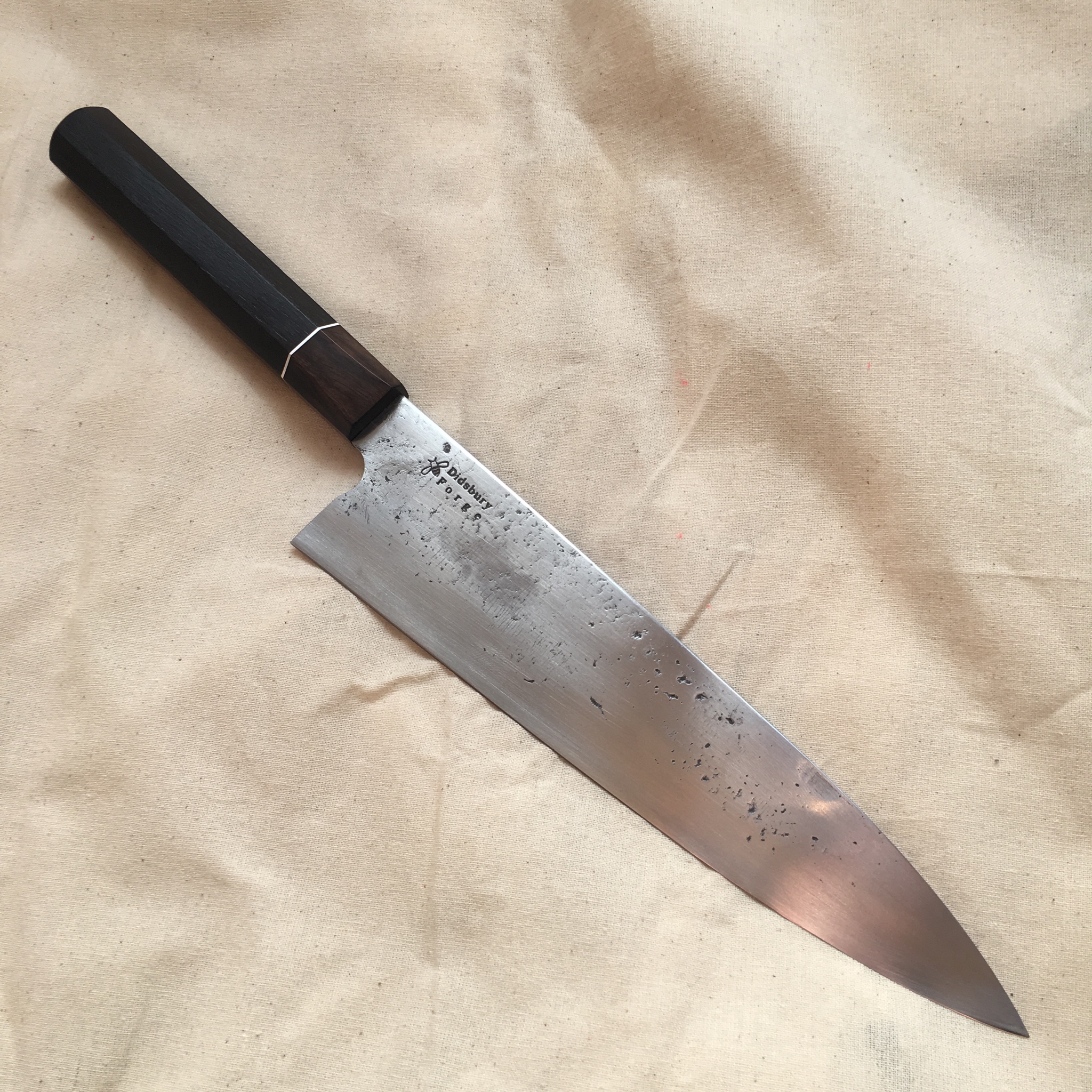
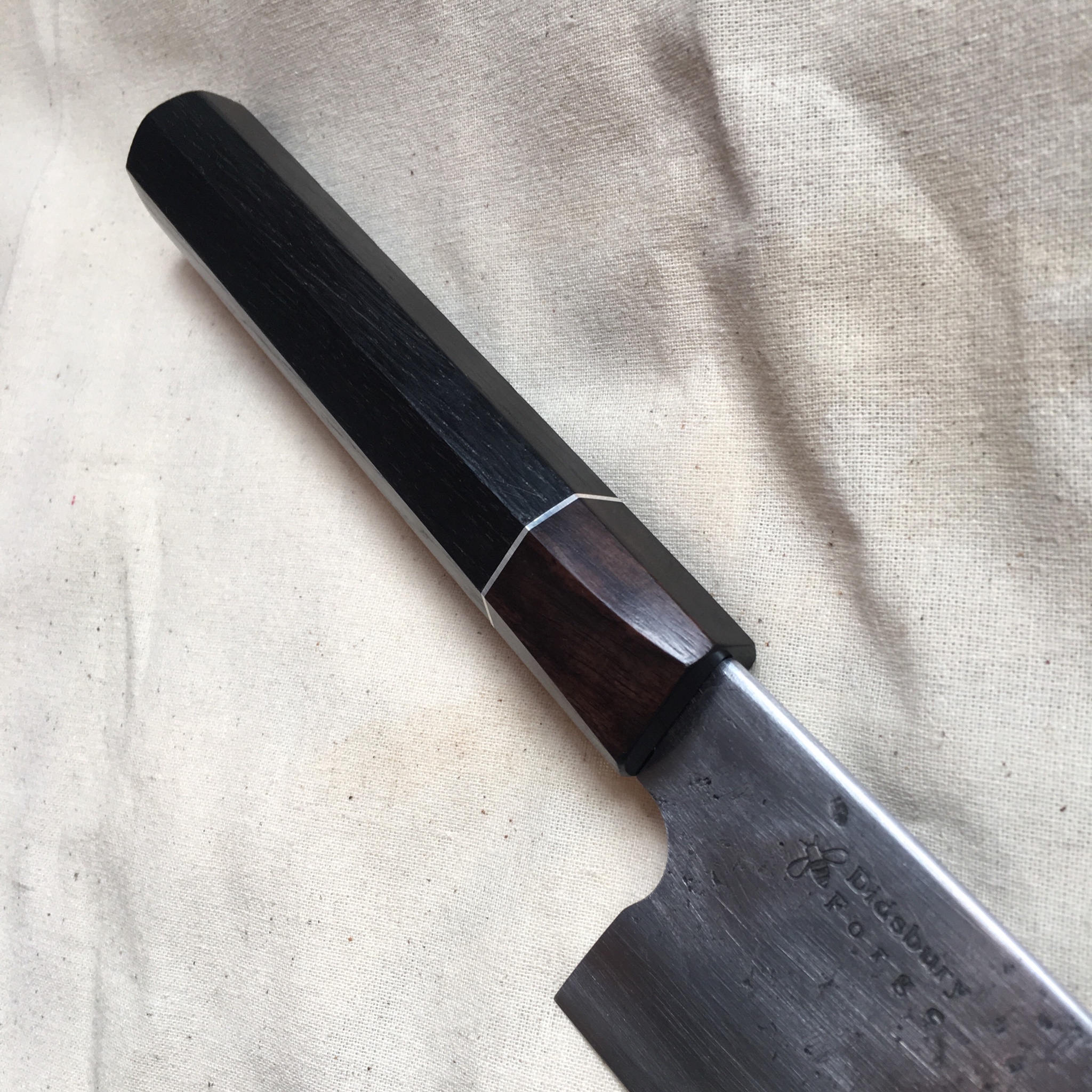
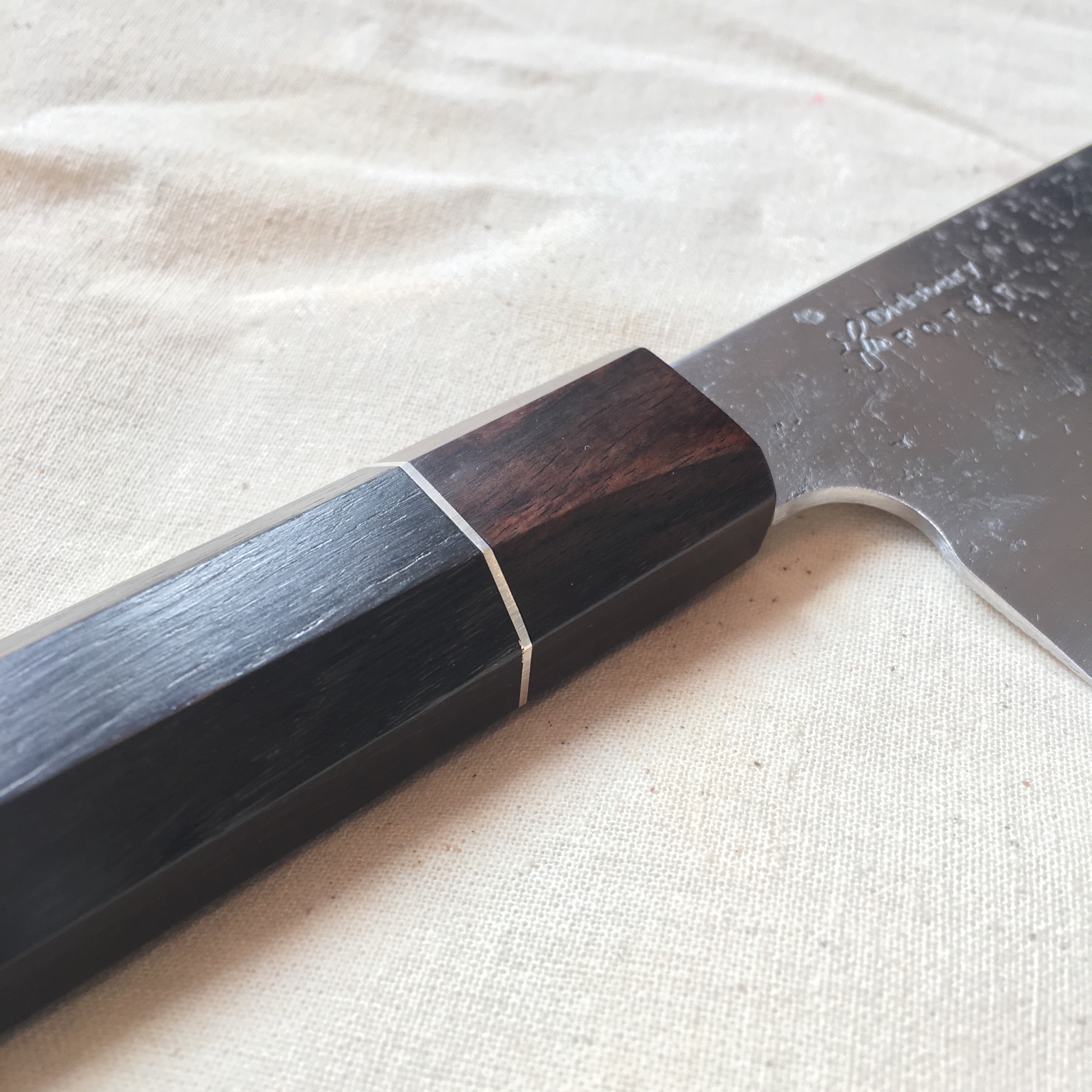